Diese Seite befindet sich noch im Aufbau!
Die Technik im Einzelnen:
1. Elevatoren
Elevatoren dienen dem Transport von Getreide und Mahlgut. Sie laufenin Holzkanälen und können deshalb eigentlich nicht in Funktion beobachtet werden. Das Bild zeigt ihren Aufbau: kleine Becher sind auf einem über ein Antriebsrad laufendes Textilband befestigt.
Die Becher nehmen im unteren Bereich das Getreide/Mahlgut auf und transportieren es zur weiteren Verarbeitung nach oben (zum Aspirateur, zum Trieur, zum Plansichter). Angetrieben wird jeweil die obere Welle über einen Riemen. Die Größe der Riemenscheibe bestimmt die Geschwindigkeit des Elevators.
2. Schnecke
Wird der Transport des Mahlgutes in horizontaler Richtung notwendig, dann werden dazu Schnecken eingesetzt: ein Metallband, das schneckenförmig auf einem eisernen Kern angebracht ist. Auch die Schnecken werden über Riemenscheiben angetrieben. Die antreibende Riemenscheibe hat dabei meist nur einen geringen Durchmesser, weil der horizontale Transport mit geringen Geschwindigkeiten bewerkstelligt werden kann.
3. Aspirateur
Vom Einfülltrichter im Boden des Erdgeschosses bringt ein Elevator das Getreide zunächst zum Aspirateur. Dort wird der vorhandene Staub abgesaugt und mit Hilfe von zwei unterschiedlich feinen Drahtsieben werden “Schrollen” (Erdklümpchen vom Acker) und Sand von Getreide getrennt.
4. Trieur
Das vom Aspirateur kommende Getreide wird mit einem weiteren Elevator zum Trieur transportiert. Der Trieur (frz. “Ausleser”) trennt das Getreide von unerwünschten Samenkörpern der Ackerunkräuter, die beim Ernten unbeabsichtigt in das Getreide gelangen. Der Trieur nutzt dabei die Tatsache aus, dass das Getreide eine längliche Form aufweist, die Unkrautsamen aber rund sind.
5. Schälmaschine
In der Schälmaschine wird das Korn von seiner Schale getrennt. Durch das Abtrennen der Schale (in der sich Farb- und Mineralstoffe befinden) kann durch die Vermahlung des eigentlichen Mehlkernes weißes Mehr erzeugt werden. Die abgetrennten Schalen werden durch ein Gebläse zu drei großen Stoffiltern gefüht und dort in Säcken gesammelt und als Viehfutter weiterverwendet. Im Zulauf zur Schälmaschine befindet sich ein starker Dauermagnet, der verhindert, dass kleine Eisenteile (z.B. Bruchstücke eines Hufnagels) in das Mahlgut gelangen.
Das geschälte Korn wird über einen weiteren Elevator zum Schroten einem Walzenstuhl (mit geriffelter Stahlwalze) zugeführt.
6. Walzenstuhl
Im Walzenstuhl wird das gereinigte und geschälte Korn zwischen zwei horizontal liegenden Walzen vermahlen. Die erste Walze wird über eine Riemenscheibe angetrieben. Die zweite Walze wird von der ersten Walze über ein Zahnradgetriebe gedreht. Durch unterschiedlich große Zahnräder wird erreicht, dass die zweite Walze langsamer läuft als die Erste. Dadurch werden die Körner am Mahlspalt zwischen den beiden Walzen nicht nur gequetscht, sondern tatsächlich zermahlen.
Die Leistung von Walzenstühlen ist bedeutend größer, als die der klassischen Steinmahlgänge und ihre Wartung ist bei weitem weniger aufwändig. Deshalb wurde zur weiteren Verarbeitung des Mahlgutes nach dem Schroten zusätzlich zu den vorhandenen Steinmahlgängen ein Walzenstuhl mit Porzellanwalzen eingebaut. Er funktioniert nach dem gleichen Prinzip wie der oben beschriebene, aber durch die Verwendung von sehr frein strukturierten Porzellanwalzen ist dieser Walzenstuhl besonders für das Ausmahlen von feinem Mehr geeignet.
Das Mahlgut wid nach dem Schroten mit einem Elevator zum Plansichter transportiert.
Beide Walzenstühle werden durch eine besondere Einrichtung entlüftet, um eine ggf. sonst mögliche Staubexplosion zu verhindern. Dazu ist im Dachgeschoss ein Ventilator eingebaut, der den feinen Mehlstaub über Holzkanäle vom Ausgang der Walzenstühle absaugt und in vier Stofffiltern sammelt. Von dort wird das Mehl über einen Holzkanal in regelmäßigen Abständen in den Mahklreislauf zurückgeführt.
7. Plansichter
Der Plansichter ist im obersten Geschoss der Mühle, direkt unter dem Dachspitz untergebracht. Er wird mit Hilfe eines Excenters über eine Riemenscheibe im darunter liegenden Geschoss angetrieben. Die 12 Siebebenen des Plansichters trennen mit Hilfe von unterschiedlich feinen Draht- und Textilsieben die verschiedenen Körnigkeiten des Mahlgutes in Mehl, Dunst, Feingrieß und Grobgrieß. Was nicht fein genug gemahlen ist, wird über den “Überlauf” zu den Steinmahlgängen oder zum Walzenstuhl mit Porzellanwalze zurückgeführt und dort weiter vermahlen.
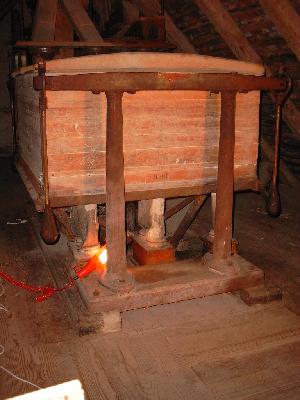
Das gilt auch für Grieß und Dunst, wenn nur Mehr erzeugt werden soll. Der Plansichter stellt neben der Schälmaschine den damaligen entscheidenden technischen Fortschritt dar, weil mit ihm verschiedene Mahlgerade unterschieden werden können, während z.B. ein Beutelsichter entsprechend seiner textilen Struktur nur eine einzige bestimmte Mehlsorte aussieben kann.
Nach jedem weiteren Mahlgang wird das Mahlgut erneut mit einem Elevator zum Plansichter geführt und dann entsprechend der gewünschten Feinheit über Holzkanäle zur darunter liegenden Absackstation gebracht oder eben erneut wieder vermahlen.
8. Steinmahlgang
Ein Steinmahlgag besteht aus einem festliegeden Bodenstein und einem sich drehenden Läuferstein. Der Läuferstein wird dabei über ein Getriebe von zwei Kegelrädern im darunter liegenden Geschoss angetrieben. Interesssant ist in dem Zusammenhang, dass das größere Kegelrad auswechselbare Holzzähne hat, die im Falle einer Störung zwar leicht brechen (und damit den Mahgang sillsetzen), aber problemlos und schnell ersetzt werden können.
Der Abstand zwischen den beiden Steinen kann je nach anfallender Arbeit größer oder kleiner gemacht werden. Die Steine werden von einer Zarge abgedeckt. Das Mahlgut wird, vom Plansichter kommend, mit Hilfe einer Schnecke zum Mahlgang transportiert und dort über einen Trichter zugeführt. DI´ie in den Mahlgang fließende Menge wird über einen “Rüttelschuh” gesteuert, der von einem mitdrehenden “Dreischlag” bei jeder Steinumdrehung dreimal angestoßen wird. Stärkere Neigung des Rüttelschuhes und stärkere Stöße durch den Dreischlag ergeben dabei einen höheren Zufluss an Mahlgut. Wird der Rüttelschuh flacher eingestellt, bzw. die Stoßkraft des Dreischlages gemindert, fließt dementsprechend weniger Mahlgut zu. (Der zweite Mahlgang hat statt des “Dreischlage” einen “Vierschlag”).
Durch die Drehbewegung des Läufersteines und durch den entsprechenden “Schliff” beider Steine wird das Mahlgut zerkleinert und gleichzeitig nach außen geführt. Das am Mehlloch austretende Mahlgut wird zuerst mit einer Schnecke und dann mit einem Elevator zum Plansichter gebracht.
Zur Wartung (z.B. zum Schleifen) der schweren Mahlsteine kann der Läuferstein mit Hilfe eines Steinkranes abgehoben werden. Durch ein Gewinde wird die dazu benötigte Kraft soweit reduziert, dass der Läuferstein ohne große Mühe von einer Person abgehoben werden kann.
Die beiden Steinmahlgänge sind die ältesten Teile der Mühle. Bereits beim Bau im Jahr 1750 wurden sie nachweislich in der Mühle eingerichtet. Da aber Steinmahlgänge beim Betrieb einem natürlichen Verschleiß unterliegen, sind sie sicher seither mehrfach ausgetauscht und erneuert worden.
9. Antriebswellen, Räder und Riemen
An einigen Stellen sind Zahnräder zu Kraftübertragung eingesetzt. Weitaus mehr sieht man aber Riemenscheiben und Riemen zur Weiterführung der durch Turbine oder Elektromotor erzeugten mechanischen Energie. Dabei entstand durch den Einbau der komplizierten Mühlentechnik in das vorhandene Gebäude ein scheinbar unüberschaubares Gewirr von Achsen, Rädern und Riemen. Bei näherem Hinsehen erkentt man aber, wie genau alles geplant und geordnet werden musste, damit diese MÜhler über Jahrzente hinweg betrieben werden konnte. Es ist erstaunlich mit welchem Geschick und mit welchen umfangreichen technischen Kentnissen die Erbauer dieser Mühle vorgegangen sind. Die Hauptantriebswelle im Erdgeschoss, mehrere kleine Antriebswellen im Obergeschoss, große und kleine Riemenscheiben, breite und schmale Riemen, alles wurde so eingeordnet, dass jedem Gerät immer genau die benötigte Energie zur Verfügung steht. Dazu bedarf es aber einer ständigen Wartung und Pflege der gesamten Anlage. Unzählige Schmierstellen an den Achsen und an den Geräten müssen regelmäßig versorgt werden. Die Pflege der Riemen und der Riemenscheiben ist ebenfalls aufwändig, auch weil die Witterung für die Riemenhaftung eine nicht zu vernachlässigende Größe darstellt (Luftfeuchtigkeit, Wärme).